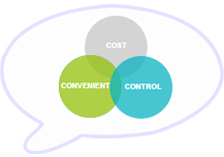
Asphalt recycling technologies
As we know, researcher Decker listed five methods using RAP: cold recycling in plant, hot recycling in plant, cold in place recycling, hot in place recycling, RAP recovery. In fact, the last method is hardly used. In the remaining four methods, each method will provide different advantages and disadvantages, and the selection of appropriate methods should be particularly considered in specific terms where applicable.
Hot recycling in plant: this is the most common type of asphalt recycling and is now considered standard asphalt paving practice. There are abundant technical data available indicating that properly specified and produced recycled hot mix asphalt is equivalent in quality and structural performance to traditional hot mix asphalt in terms of rutting, raveling, weathering, and fatigue cracking. Recycled hot mix asphalt mixture also generally age more slowly and are more resistant to the action of water than traditional hot mix asphalt. Recycling in plant is able to produce hot mix asphalt containing up to 100% RAP depending on kinds of plants and RAP quality. This technology consists of next basic processes: old pavement milling and storage in plant, mixing with virgin materials to produce HMA and paving. In this technology, RAP is heated directly by a specific dryer.
Cold recycling in plant: cold recycling in plant is similar to hot recycling in plant excepting the way to heat RAP. In cold recycling in plant RAP is heated indirectly through superheated aggregates. The quality of HMA using this technology is equivalent traditional HMA in above listed characteristics and performance. The maximum limit for RAP content in this technology is up to 50% depending on kinds of plants and RAP quality. This technology consists of next basic processes: old pavement milling and storage in plant, mixing with virgin materials to produce HMA and paving
Fig. 1 – Asphalt recycling technology in batch mixing plant at BMT
Hot in place recycling: the use of hot in place recycling has developed rapidly over the past decade, although it is in use only on a limited basis. The major advantage of this technology is the cost saving for transporting, processing and stockpiling RAP. The major disadvantage of this technology is the inability to make significant changes to the mix. Pavements that exhibit structural base failure, irregular patching or the need for major drainage or grade improvements are not suitable candidates for cold in place recycling. Geographically, this technology is suitable for repairing the roadways in remote areas, where is not convenient to set up the mixing plant. The cold in place recycling consists of three processes: heater-scarification, repaving and remixing.
Cold in place recycling: is similar to hot in place recycling in recycling methodology and processes. The only difference is that for this technology RAP is not heated at all, but is mixed directly with additives such as emulsion, foam bitumen, etc. This technology consists of next steps: old pavement milling, mixing it with recycling agents and virgin materials, repaving.
Fig. 2 – The machinery system of cold recycling technology of Roadtec
Thus, to select the appropriate method for recycling we need to consider many factors: geographical, technical, economic, human, weather, etc. and it’s necessary to refer the use of other countries. According to the Europe Asphalt Pavement Association (EAPA) in 2011, in some developed countries, the amount of RAP is used with very large volumes, up to 70% in Japan, 85% in Canada on the national total asphalt production. Among recycling technologies, hot mix recycling is always the top selection, dominating the overall recycling output. In Australia, the U.S., Germany and Canada over 80% recycled asphalt is produced using hot mix recycling.
Dr. Vo Dai Tu