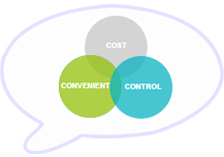
Overview of reclaimed asphalt pavement
Studies on the economic and environmental issues have promoted recycling steel, aluminum, plastics and other materials. Among them, the asphalt pavement is one of the recyclable materials, which is widely applied by researchers and investors around the world for a long time. According to researcher Taylor, reclaimed asphalt pavement (RAP) was mentioned in 1915, but it was not widespread. By 1970, the need to use RAP becomes practical due to the increase in the cost of asphalt and the scarcity of stone materials. The problems related to the economy and the environment has spurred the development of production technology asphalt containing RAP [1].
According to researcher John Sullivan, in the 70s of the 20th century there were about 10 million tons of RAP (33% respectively) are used, allowing a significant reduction of asphalt costs while satisfying features and the technical criteria [2].
Decker D.S. listed 5 methods using RAP: cold recycling in plant, hot recycling in plant, cold in place recycling, hot in place recycling, RAP recovery [3]. As reported by the Minnesota Department of Transportation, hot mix recycling technology is a method commonly used and most effective due to the following advantages [4]:
1) Simplicity in quality control as traditional hot mix asphalt;
2) 20-30% cost saving;
3) Do not waste stone and bitumen resources;
4) Do not pollute the environment.
Fig. 1 – Green logo claiming the quality of reclaimed asphalt pavement of Virginia Asphalt Association
According to the Shell Group currently has 80-90% of the RAP is put into recycling in Germany, the U.S., Belgium, Netherlands, Luxembourg, 50-60% in China, Slovenia, Sweden, Switzerland and Denmark. In the recycling process, ranging from 20-35% RAP included in the mixture mixed with virgin materials. There are already many plants in Europe, Japan, etc. being able to produce HMA containing RAP up to 100% RAP. Asphalt hot mix recycling has entered the commercial stage from the last decade of the twentieth century. In 2006, in Germany, Luxembourg, Netherlands HMA containing RAP occupied up to 90% of asphalt national total quantity.
Fig. 2 – RAP reuse in various countries
Hot mix asphalt recycling technology and its design methods is now no longer a secret of any agency or country. In Europe, over 95% of asphalt mixing plant is designed to be able to use the RAP. RAP design methodology can be found more easily in the open documents on the Internet. The most common method is Superpave designed by John Bukowski. In 2001, based on the method of Bukowski, Transportation Research Institute National American has launched HMA design standards containing RAP. In 2002, the Minnesota Department of transportation design standards issued by both methods RAP Superpave and Marshall / Hveem [4]. European published technical standards EN 13,108-8 for HMA containing RAP in 2005. In addition, through the process of research and test a few roads in the state of Florida, a group of researchers Sungho Kim, Thomas Byron, Gregory A. Sholar, Kim Jaeseoung of Florida Department of Transportation also announced the design standards contained RAP REV BTN 1-17-2, 2-6-12 FA in report in 2007.
Fig. 3 – Hot mix asphalt recycling in plant
Although recycling technology has been widely applied in many countries around the world, but this technology is still a new thing for our country. In the using process due to the effects of the repeated load as well as of the influence of environment it’s impossible to avoid damage, so the pavements need to repair, upgrade and enhance. Now, solution of our country is landfilling old asphalt pavement and replacing with new asphalt layer or coating new layer directly on the old pavement.
According to the actual situation, the amount of RAP today in our country is still not reused and becomes industrial wastes, burdening the environment. These solutions lead to more adverse problems for economy and environment such as: waste materials, environmental pollution, depletion of natural stone and bitumen.
1. Taylor, N. H., “Life Expectancy of Recycled Asphalt Paving,” Recycling of Bituminous Pavements, L.E. Wood, ed., ASTM STP 662, American Society of Testing and Materials, Philadelphia, Pennsylvania, 1978, pp. 3-15.
2. Sullivan, J., “Pavement Recycling Executive Summary and Report,” FHWA-SA-95-060, Federal Highway Administration, Washington, D.C., March 1996.
3. Decker, D. S., “State of the Practice for use of RAP in Hot Mix Asphalt,” Journal of the Association of Asphalt Paving Technologists, Volume 66, 1997, pp. 704.
4. Michael S. Sondag, Bruce A. Chadbourn, Andrew Drescher. Investigation of recycled asphalt pavement (RAP) mixtures. Minnesota Department of Transportation. Final report 2002. 94 p.
Dr. Vo Dai Tu