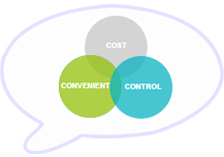
SUPERPAVE MIX DESIGN
One of the principal results from the Strategic Highway Research Program (SHRP) was the Superpave mix design method. The Superpave mix design method was designed to replace the Hveem and Marshall methods. The volumetric analysis common to the Hveem and Marshall methods provides the basis for the Superpave mix design method. The Superpave system ties asphalt binder and aggregate selection into the mix design process, and considers traffic and climate as well. The compaction devices from the Hveem and Marshall procedures have been replaced by a gyratory compactor and the compaction effort in mix design is tied to expected traffic.
Nowadays, the most advanced design method for hot mix asphalt (HMA) is known as the Superpave. Superpave is shortened from the phrase Superior performance asphalt pavement, which was developed to replace the Hveem and Marshall methods. The volumetric analysis common to the Hveem and Marshall methods provides the basis for the Superpave mix design method. The Superpave system ties asphalt binder and aggregate selection into the mix design process, and considers traffic and climate as well. The compaction devices from the Hveem and Marshall procedures have been replaced by a gyratory compactor and the compaction effort in mix design is tied to expected traffic.
The Superpave mix design method consists of 7 basic steps:
1) Aggregate selection;
2) Asphalt binder selection;
3) Sample preparation (including compaction);
4) Performance tests;
5) Density and voids calculations;
6) Optimum asphalt binder content selection;
7) Moisture susceptibility evaluation.
1. Aggregate selection
Superpave specifies aggregate in two ways. First, it places restrictions on aggregate gradation by means of broad control points. Second, it places “consensus requirements” on coarse and fine aggregate angularity, flat and elongated particles, and clay content. Other aggregate criteria, which the Asphalt Institute (2001[2]) calls “source properties” (because they are considered to be source specific) such as L.A. abrasion, soundness and water absorption are used in Superpave but since they were not modified by Superpave they are not discussed here.
The stone aggregate with good angularity, suitable for HMA in accordance with Superpave
Coarse aggregate angularity is important to mix design because smooth, rounded aggregate particles do not interlock with one another nearly as well as angular particles. This lack of interlock makes the resultant HMA more susceptible to rutting. Coarse aggregate angularity can be determined by any number of test procedures that are designed to determine the percentage of fractured faces. Superpave specifies closely the angularity of coarse aggregate and fine aggregate for each traffic class of road layers.
In order to ensure the proper amount of material passing the 0.075 mm (# 200) sieve in the mix design, Superpave specifies a range of ratio of #200-material (P200) to effective binder content (Pbe). Usually, the ratio P200/Pbe is specified in the range 0.6 ÷ 1.2, but a ratio of up to 1.6 may be used at an agency’s discretion.
2. Asphalt binder selection
Superpave uses its own asphalt binder selection process, which is, of course, tied to the Superpave asphalt binder performance grading (PG) system and its associated specifications. Superpave PG asphalt binders are selected based on the expected pavement temperature extremes in the area of their intended use. Superpave software (or a stand-alone program such as LTPPBind) is used to calculate these extremes and select the appropriate PG asphalt binder using one of the following three alternate methods: pavement temperature; air temperature; geographic area.
PG system classifies asphalt binder according to 2 numbers: the maximum and the minimum working temperature of the binder. Based on the average temperature of the pavement in different time, the asphalt binder can be selected according to PG system.
PG grades for different crude oil blend
3. Sample preparation
The Superpave sample is prepared using the Gyratory Compactor with compaction pressure 600 kPa. The Superpave sample size is 150 mm diameter cylinder approximately 115 mm in height. The number of blows is variously specified according to different traffic levels.
![]() |
![]() |
Gyratory Compactor |
The Superpave gyratory compactor sample (left) vs the Marshall compactor sample (right) |
4. Performance tests
Currently, the Superpave performance tests are still under development and review and have not yet been implemented. Some Superpave performance tests are known such as dynamic modulus, wheel tracking depth, fatigue and cracking resistance, moisture susceptibility.
![]() ![]() |
![]() |
Hamburg wheel tracking test |
Dynamic modulus test |
5. Density and voids calculations
As the other mix design methods, the Superpave also analyzes density and voids to determine the characteristics of hot mix asphalt.
6. Optimum asphalt binder content selection
The optimal asphalt binder content is determined according to the values of air voids, voids in the mineral aggregate (VMA) and voids filled with asphalt binder (VFA). The optimal asphalt binder content is selected that asphalt binder content that results in 4 percent air voids at the designed number of blows.
7. Moisture susceptibility evaluation
Moisture susceptibility testing is the only performance testing incorporated in the Superpave mix design procedure as of early 2002. The modified Lottman test is used for this purpose.
Dr. Vo Dai Tu
Research – Development & Testing Department