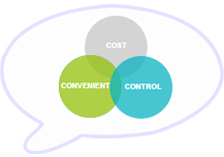
Modified bitumen BMT-ATR – Effective antirutting agent
Among causes of rutting on the asphalt pavements, bitumen is the first factor needed to be improved, especially in the tropical climate condition and heavy traffic in our country.
Traditional 60/70 grade bitumen has low softening point (the softening point of the best quality 60/70 bitumen in Vietnam is about 48oC) and low thermal stability (PI negative). In addition, traditional bitumen refined from crude oil almost has not have elasticity, so that it can bear heavy load with high frequency repetition.
One of the solution submitted by experts for improving thermal susceptibility of asphalt binder is using lower penetration grade bitumen (typically 40/60 grade). However, It’s necessary to consider that 40/60 grade bitumen belongs to hard bitumen. It can only improve the thermal susceptibility and hardness of hot mix asphalt, but it is not an effective anti-rutting agent under heavy load with high frequency repetition because of lack of elasticity. Besides, it’s well-known that the cohesion between acid aggregates, such as granite, with bitumen refined from crude oil is very low (level 3 for the best aggregate in south of Vietnam). Hamburg wheel tracking test in water bath showed that the rutting depth of hot mix asphalt using traditional bitumen is very high (about 15 mm) and many specimens are even destroyed and fully stripped.
It has been known that rutting can be prevented due to the application of modified bitumen in hot mix asphalt. In recent times, we have applied PMB – a kind of bitumen modified with block copolymer SBS as new binder to increasing rutting resistance of asphalt pavement. According to laboratory testing and road paving for many projects, BMT experts confirmed that PMB improves technical characteristics of asphalt pavement, but it doesn’t give high economy effect because of extremely high cost. Totally, PMB is not an appropriate solution for our country nowadays.
Understanding difficulty in research the best anti-rutting solution satisfying both technical and economic requirements, Dr. Vo Dai Tu and colleagues have developed and successfully produced modified bitumen BMT-ATR – the best anti-rutting agent with the remarkable economic effect in our country.
Fig. 1 – Chemical structure of modifying additive in composition of BMT-ATR
BMT-ATR is a modified bitumen of BMT Construction – Investment J.S.C., which is used to improve thermal stability and rutting resistance of hot mix asphalt. According to chemistry composition, BMT-ATR is a bitumen modified with vulcanized thermoplastic copolymers and additives (non SBS). These polymers link to hydrocarbon molecules of bitumen due to physical chemistry bonds in the presence of additives, which forms a homogenous colloidal system with remarkable properties. BMT-ATR improves rutting resistance of asphalt to heavy load at high temperature. Besides, BMT-ATR improves resistance to plastic deformation due to increasing binder elasticity, moisture susceptibility, and shear resistance of hot mix asphalt. BMT-ATR is suitable to apply in road and bridge projects with heavy traffic and high frequency load repetition, in the regions with tropical climate and water damage.
Fig. 2 – The minimum softening point of various bitumen grades
Nowadays, in conditions in our country BMT is developing 2 grades of BMT-ATR: BMT-ATR-1 and BMT-ATR-2 corresponding to detail traffic conditions.
BMT-ATR-1 has higher quality than 60/70 grade bitumen. It is appropriate for:
- High strength dense grade hot mix asphalt;
- Highway belong to class A1 & A2; national routes, inter-province routes;
- Heavy traffic lane;
- Pavement in regions with high temperature and high water damage.
Fig. 3 – Rutting depth of hot mix asphalt (grade 9.5) using BMT-ATR-1 and 60/70 grade – HWTD testing in air condition at 60oC
BMT-ATR-2 has higher quality than BMT-ATR-1 and comparable with PMBI. It is appropriate for:
- High strength dense grade hot mix asphalts;
- Gap grade, open friction grade hot mix asphalts;
- Stress absorbing membranes (SAM) and Stress absorbing membrane interlayers (SAMI);
- Expressway, extreme heavy traffic road;
- Taking off and landing runways, ports.
Fig. 4 – Rutting depth of hot mix asphalt (grade 19) using BMT-ATR-2 and PMBI – HWTD testing in water condition at 50oC
Fig. 5 – Specimen photos after rutting testing using Hamburg wheel tracking device